Gradually the need for wholesale bottled milk
delivered direct to dairymen locally, led to the
start of bottling at Rooksbridge. In the early days, much of this would have been
labour intensive! The early bottles would have been filled individually
and a large waxed cardboard cap would have been pressed into the top of
the bottle.
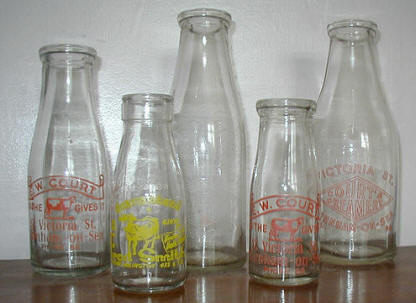 |
Examples of early milk bottles. From half pint to
quart sizes. (Including centre: an unusual, one and a half pint
bottle) from E W Courts Dairy in Victoria St. Burnham on Sea.
The large neck bottles with a
cardboard cap insert were used up until the 1950's
The yellow labelled bottle is an example of an
early foil capped half pint.
Photo. J Rigarlsford |
During the 1950's the foil capped bottle as we know it became
standard. By having the foil cap crimped over the top of the neck this
was much more hygienic than the old cardboard insert caps. (The foil
caps though are easier for blue-tits etc to open! And they have
always had a preference for full cream Channel Island milk)!!
Over the years, improved and faster bottlewashing and filling
machinery were installed at the dairy, including machinery for filling cartons etc. Also
the old heavy gauge bottles and steel crates were slowly phased out in
favour of lighter weight "Dumpy" bottles and plastic crates.
Photo: R Brown |
In the late 1960's a brand new 'Bottling Hall' was built on land next
to the dairy. Forklift trucks were first introduced with the new bottling set-up. These
latter improvements were a godsend to the bottling staff and drivers,
whose life until then, consisted on heaving everything about by hand!
Photo: R Brown |
In theory the bottling would be fully automatic. From the
de stacking of the empties through the washing and filling the bottles
to restacking the full crates at the other end!
As always, theory and fact are never quite
the same! And each part of the bottling process still had to be
monitored by operators. One of the biggest problems was picking out any
bottles that had been returned dirty, or contained foreign objects and
preventing these from entering the process!
(Its sometimes surprising what turns up back at the dairy in a
bottle)!
At one time, the
operators had a display of 'Unusual Foreign Objects'... Some
more unsavoury than others!
Here we see
the de-crater, where the returned milk bottles were removed from the
crates in preparation for washing and refilling.
The operator is looking for and removing bottles that cannot be
effectively cleaned because they contain foreign objects or bottles from
building sites etc. that have not been properly rinsed and
'foreigners' (ie. non standard and bottles belonging to other
dairies etc).
Photo: R Brown |
Bottlewasher infeed.
The returned bottles
pass over a series of high pressure jets before emerging
at the other end clean
and sterilised, ready for refilling.
Photo: R Brown |
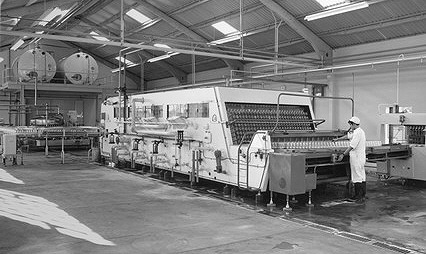 |
|
A general view of
the outfeed, filler-capper and re-crating area.
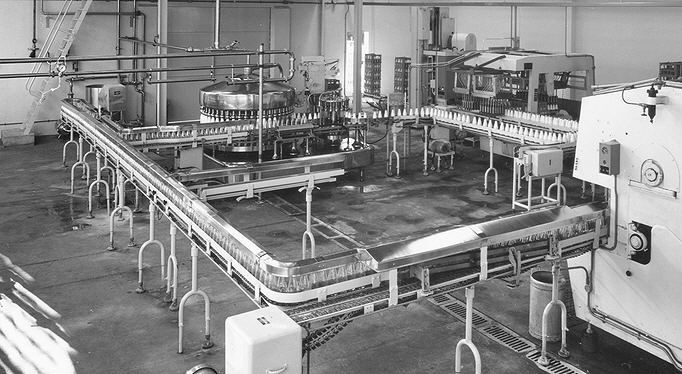 |
Photo: R Brown
High speed bottle filler
The filler-capper was
designed to fill, up to 400 bottles per/min.
But a more realistic
figure for the whole process was an average of around 330 Bottles
per/min or 1000 crates an hour.
Photo: R Brown |
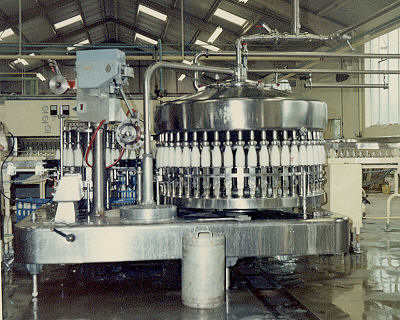 |
The regrouper
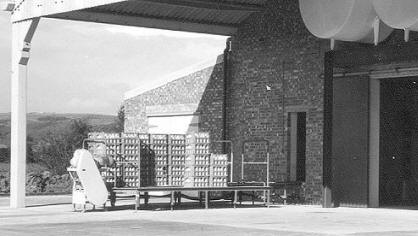 |
After refilling, from
here, stacks of full crates were loaded by forklift onto lorries
for distribution. Or stored in the coldroom. Photo: R Brown |
Bottle Transport Until
the phasing out of farm churn collections in the early 1970's, Bottled
milk was generally transported on the flatbed lorries which were also
used for farm collection. Eventually these were replaced by specialised
refrigerated vehicles which eliminated the problems of frozen milk in
winter and warm milk in summer! and allowing bottled milk to be
delivered in good condition over a wider area.
Circa: 1970. A typical load of milk being
transported open to the elements! Photo: R Brown |
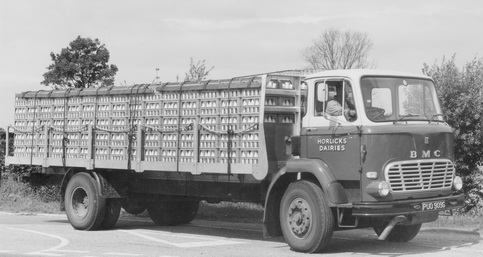 |
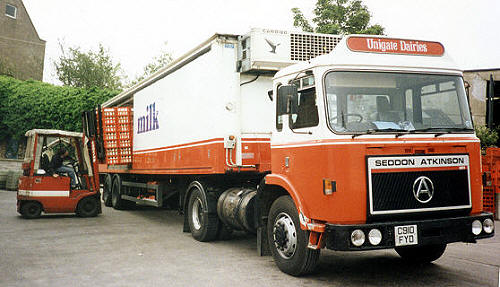 |
Circa: 1990. And specialised refrigerated
vehicles enabled bottled milk to be moved over far greater
distances.
Photo: J
Rigarlsford. |
|